What is a Gravimetric blender
Gravimetric blender are used in the injection and extrusion industries. This is an automatic equipment that can automatically weigh and automatically mix various raw materials that need to be mixed in precise proportions. This is a mechanical device that integrates weighing, metering and mixing functions. The Gravimetric batch blender will weigh the raw materials proportionally by weighing and measuring the degree, and then enter the mixing tank for raw material processing. High-speed impact and dispersion can achieve rapid mixing, dispersion and refinement of functional and efficient equipment. The measurement can be accurate to particles, and the mixing accuracy can be as high as ±0.1%. One equipment adopts PLC controller, which can mix multiple raw materials at the same time after accurate weighing and mixing. It has advanced batching algorithm, excellent production performance, automatic alarm and error correction function, stable operation, safe and reliable comprehensive technical characteristics. Technology to solve manual weighing errors and uneven mixing in production.
Especially in the medical and environmental protection industries, the machinery will fully adopt food stainless steel materials and fully enclosed feeding and discharging to avoid external pollution.
There are many types of gravimetric blender.Non-standard type and standard type, but there are two most common types
Loss in weight
This type of gravimetric blender measures the "loss in weight" from two or more hoppers using a load cell under each hopper. Material is usually dispensed from the hoppers using a screw conveyor. All materials are dispensed together and the rate of dosing from each hopper is controlled to ensure the correct blend is achieved.
Gain in weight (sometimes called a batch blender)
A gain in weight gravimetric blender has two or more hoppers arranged above a weigh-pan. These hoppers contain the components which are to be mixed, at the base of each hopper there is a valve to control the dispensing of material from the component hopper into the weigh-pan. The components are dispensed one at a time into the weigh pan until the target or batch weight is reached. Once the batch has been weighed out the contents of the weigh-pan are dispensed into a mixing chamber where they are blended. The resulting mixture exits the base of the mixing chamber into the processing machine.
A typical application of a gravimetric blender would be mixing virgin plastic granules, recycled plastic, and masterbatch (an additive used to colour plastics) together.
The gravimetric batch blender provides precise batch-to-batch dispensing and consistent homogenous blending. Standard features include off-the-shelf controls, color touch-screen, removable cartridge V-gate metering, segmented material hoppers, integral drain chute, and a “no dead zone” mixing chamber. The blender may be configured with 4-12 ingredient hoppers, with each hopper capable of running 0-100% of the recipe with dispensing accuracy up to +/-0.01%, with throughput rates to over 10,000PPH.
Composition of Gravimetric blender:
The main components of the Gravimetric blender include hoppers, racks, weighing instruments, mixing barrels, PLC consoles, electric boxes, motors and other components.
Schematic diagram of Gravimetric blender
1. Upper hopper, 2. Display, 3. Unloading cylinder, 4. Controller, 5. Mixing box, 6. Observation window, 7. Lowering cylinder, 8. Discharge valve, 9. Sub-hopper, 10. Motor, 11. Feeding port of sub-hopper, 12. Feeding port of sub-hopper, 13. Pull plate, 14. Cylinder assembly box, 15. Weighing hopper, 16. Horizontal screw, 17. Mixing hopper.
detailed description
The Gravimetric blender includes an upper hopper 1, a mixing box 5, a lower hopper 7 and a controller 4 connected in sequence. The upper hopper is divided into a plurality of sub-hoppers 9 by partitions, each of which is The upper part of the hopper is provided with a sub-hopper feed port 11, and the bottom is provided with a sub-hopper discharge port 12. Below the sub-hopper discharge port in the mixing box, a cylinder assembly box 14, a weighing hopper 15 and a mixing hopper 17 are sequentially installed. A plurality of blanking cylinders 3 are installed on the cylinder assembly box, and the connecting rod of the blanking cylinder is provided with a pull plate 13 corresponding to the discharge port of the corresponding hopper, and a weighing plate is provided under the pull plate. A device (not shown), a horizontal screw 16 driven to rotate by a motor 10 is installed in the mixing hopper, a timer (not shown) and a discharge valve 8 are installed at the discharge port of the mixing hopper, and the controllers are respectively It is electrically connected with multiple blanking cylinders, multiple weighing devices, timers, motors and discharge valves, receives information from each weighing device, controls the actions of the corresponding blanking cylinders, opens or closes the pull plate, and receives the timer Information, control the action of the motor and the opening or closing of the discharge valve.
Further, a display 2 is installed on the mixing box, and the display is electrically connected to a plurality of weighing devices and timers.
Further, observation windows 6 are respectively provided on the plurality of the hoppers and the lower hoppers. Put the raw materials to be produced into the hopper, and then weigh or measure the raw materials according to the parameters set by the PLC console. Then the raw materials enter the mixing tank. Set the mixing time and operating speed parameters in the console, then control the complete mixing, and then execute it by the PLC. Automatic discharge speed, complete weighing and mixing |
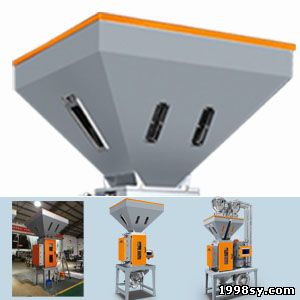 |
Gravimetric blender Upper hopper:This is the hopper of the Gravimetric blender, installed on the top of the equipment. Used to store the raw materials to be mixed. And can be equipped with multiple hoppers. Electronic funnel can be equipped as required |
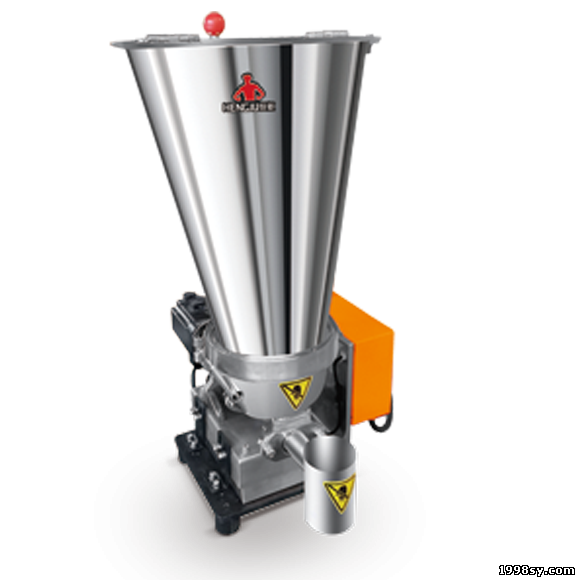 |
Gravimetric blender Screw Weight Loss Scale:Single screw weight loss scale is an automatic weighing system for Gravimetric blender, suitable for weighing each raw material of the mixer. Between the equipment, hopper and mixing barrel, various raw materials enter the hopper. When the raw materials enter the mixing barrel, the single-screw weightlessness scale will automatically weigh or measure the raw materials. Own metering system and PLC control system can perform more accurate weighing, calculation or measurement. |
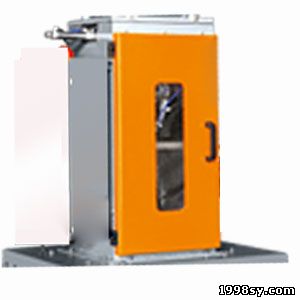 |
The mixing system is a weighing and measuring machine for raw materials in a gravimetric blender. The mixing barrel is closely connected with the hopper. This is a special mixing barrel that can mix powder and granules, powder and powder, and can be connected to PLC to control the mixing speed, time, and discharge and conveying speed. |
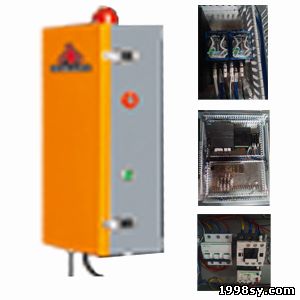 |
Electric box: This electric box is the brain of the Gravimetric blender, which controls the energy required for the operation of all components. The main switch that controls input and output devices; it is assembled from multiple components (such as integrated circuits and relays). |
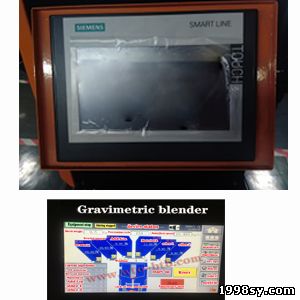 |
gravimetric blender PLC control panel: This is the mind and brain of the Gravimetric blender. It controls the operation and stop of all functions of the machine, and has functions such as automatic diagnosis, automatic warning, automatic error correction and recovery. |
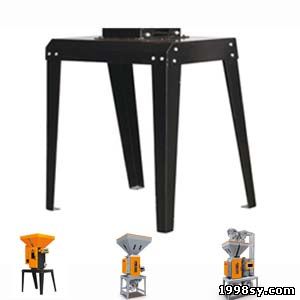 |
Gravimetric blender Bracket: This is the foot of the Gravimetric blender, which supports all the weight of the machine, and the machine is stable during operation, and the support is easy to move; |
 |
Gravimetric blender discharge barrel:The unloading barrel is installed under the mixing barrel of the Gravimetric blender and is used to store the raw materials mixed in proportion. |
Working principle of Gravimetric blender:
How Gravimetric blender works The Gravimetric blender relates to an upper hopper, a mixing box, a lower hopper and a controller connected in sequence, and relates to the technical field of feeding equipment. The upper hopper is divided into multiple sub-hoppers by part. In the mixing box, a cylinder assembly box, a weighing hopper and a mixing hopper are sequentially installed below the discharge port of the hopper. The drum assembly box is equipped with multiple unloading drums. The connecting rod of the blanking cylinder is equipped with a pull plate. There is a weighing device under the plate, the mixing hopper is equipped with a horizontally driven horizontal screw, the discharge port of the mixing hopper is equipped with a timer and a discharge valve, and the controller is connected with multiple discharging cylinders. Electrically connect the weighing device, timer, motor and discharge valve to receive information from each weighing device, control the action of the corresponding unloading cylinder, open or close the pull plate, and receive timer information to control the action of the motor and the discharge valve Turn on or off. The device provided by the utility model can automatically feed materials according to the weight ratio, and the mixing is relatively uniform.
Add a variety of raw materials to multiple hoppers, and set the corresponding parameters and mixing time of each raw material through the functions on the PLC control panel. After setting the PLC parameters, the corresponding functions will be activated. After the weighing and mixing are completed, there is a timer at the discharge port, and you can choose to control the discharge speed!
At the top of the weight mixer is an independent hopper and a weighing counter. Raw materials can enter the weighing instrument through each hopper, and then the instrument transmits the information to the parameters set in the console for automatic measurement. After weighing, the PLC console receives the information and obtains the accurate parameter value, and then transmits the information to the discharge valve switch, the discharge valve opens, and the weighed raw materials enter the mixing tank for mixing. When the raw materials enter the mixing tank, the PLC console will turn on the motor switch of the mixing tank to start mixing. At the same time, after mixing, there is a drain valve at the bottom of the mixing tank. The discharge valve is controlled by the motor speed or time parameters of the PLC console. When the time or speed reaches the mixing parameter value, the discharge valve switch opens, and the mixed material enters the following equipment.
If there are multiple raw materials, multiple hoppers must be added. You can share one meter or more. The PLC program can be programmed to control the precise weighing and uniform mixing of various raw materials. Both can be done at the same time; three raw materials, four, five, six, seven and more raw materials are mixed uniformly. |
Features of Gravimetric blender:
1. Modular and detachable structure design, saving space and easy to clean;
2. Use a dedicated weighing controller to ensure reliable performance and easy maintenance;
3. The automatic control calculation method, self-optimization and automatic adjustment function are adopted to ensure the accuracy of the ingredients (automatic correction and adjustment after each weighing. All materials are uniformly mixed after the gravity measurement, and the density can be strictly controlled). ;
4. Six kinds of raw materials can be processed at the same time;
5. Color graphic display, touch screen operation;
6. The weighing and volume mixing method increases the number of ingredients;
7. With formula storage function, 20 groups of formulas can be stored;
8. Hierarchical security password control and alarm history record function;
9. The USB data export function is optional, which is used to save the ratio data to facilitate production management;
10. It can be installed directly on the machine, or it can be installed next to the machine together with an optional tripod.
11.And equipped with automatic early warning system and automatic error correction function! If there is a material interruption during the batching of multiple raw materials, the equipment will automatically start the warning and stop the mechanical operation, the warning will sound and the warning light will flash.
12.When there is a problem with the program in production, the equipment will stop running, the warning light will sound and flash, click on the control panel of the equipment console to set-error correction-error correction success-end warning |
Model and parameters of Gravimetric blender:
Model |
HGB-50 |
100 |
200 |
400 |
600 |
800 |
2000 |
2000 |
2500 |
3000 |
Qty of group number |
4-8 |
Mixing capacity(kg/hr) |
50 |
100 |
200 |
400 |
600 |
800 |
2000 |
2000 |
2500 |
3000 |
Batch weight(kg) |
0.6 |
1.2 |
2.2 |
4.5 |
6 |
8 |
12 |
20 |
25 |
30 |
Main material range(%) |
5-100 |
Additive mixing range(%) |
0.5-10 |
Main hopper volume(L) |
18 |
25 |
32 |
45 |
70 |
100 |
130 |
160 |
180 |
230 |
Mixing barrel volume(L) |
6 |
6 |
20 |
20 |
40 |
40 |
80 |
80 |
100 |
180 |
Power supply(v/hz) |
1φ |
1φ |
1φ |
1φ |
1φ |
1φ |
3φ |
3φ |
3φ |
3φ |
|
230/50 |
230/50 |
230/50 |
230/50 |
230/50 |
230/50 |
400/50 |
400/50 |
400/50 |
400/50 |
Total power(kw) |
0.20 |
0.20 |
0.25 |
0.25 |
0.55 |
0.55 |
1.5 |
1.5 |
1.5 |
3 |
Compressed air(kgf/cm2) |
6-8 |
Max noise level(dB) |
<75 |
A new type of Gravimetric blender, used in injection molding and extrusion industries, various raw materials are accurately mixed in proportion, and the mixing accuracy can reach ±0.1%. This series of products all use PLC controllers and advanced batching algorithms to ensure the high quality and comprehensive technical characteristics of this series of products, so that the products have excellent performance, stable operation, and safe and reliable operation.
The Gravimetric batch blender is suitable for plastic injection, extrusion or hollow molding processes where a variety of raw materials need to be mixed by weight. This series of products is equipped with a microcomputer control system, and has an automatic compensation function. It can be automatically calibrated every time it is turned on with accurate accuracy and easy to learn and convenient operation. This series of products uses precision electronic scales to make the machine accurate. Choose the models according to the types of raw materials that need to be processed.
Gravimetric dosing system: This is the general term for Gravimetric blender,
The utility model relates to the technical field of mixers, in particular to an automatic gravimetric blender. Plastic parts can meet the requirements of related technical standards and expected physical and chemical properties. Automatic gravimetric blender, including a base, the base is equipped with a mixing structure, the mixing structure is equipped with a storage structure, the storage structure is equipped with a suction structure, and the mixing structure includes a lower mixing Zone and upper metering zone In this zone, the suction structure includes a suction hopper and a vacuum structure. The utility model has the advantages of accurate weight measurement of each raw material, eliminating errors in manual measurement and material transportation, and the ratio of each raw material fully conforms to the set parameters, so that different raw material components are evenly mixed in proportion. Reach a certain ratio, and finally injection molding. Plastic parts can meet the requirements of relevant technical standards and expected physical and chemical properties.
The plastic metering uniform mixing equipment adds the main and auxiliary materials to the equipment in a certain proportion, and the equipment evenly mixes and stirs the required proportion of materials, and the weighing and mixing values are more accurate. In the prior art plastic mixing, the main material and auxiliary materials are manually weighed in a certain proportion, then poured into the mixer and stirred, and finally transferred to the heating cylinder of the injection molding machine. Therefore, the main material must be added to. Weighing in proportion to auxiliary materials is inefficient, and the operation is very troublesome, and continuous mass production is impossible. The new weighing and mixing equipment will solve many problems. Automatic feeding, automatic weighing, automatic mixing and automatic unloading. Due to the software digital program system, the weighing error is very accurate, and the particles can be accurate to the particles. Make the blend value more accurate.
This is a sealed Gravimetric batch blender dedicated to medical or environmental protection products, made of food-grade stainless steel. Automatic weighing and mixing are sealed to reduce external contamination of raw materials,Modular and detachable structure design, saving space and easy to clean;
Use universal PLC controller to ensure reliable performance and easy maintenance;
Adopt advanced control algorithm, independent optimization, automatic adjustment compensation and vibration prevention functions to ensure the best batching accuracy;
The standard model can handle up to four components (more than six components can be customized);
Color graphic display, touch screen operation, multiple languages for selection;
With formula storage function, it can store more than 100 groups of formulas at most;
Hierarchical security password control and alarm history record function;
The controller is equipped with a standard USB2.0 interface, which can save the mixing ratio data to the U disk, which is convenient for production quality control;
With sound and light alarms, it is convenient for the equipment personnel to quickly and accurately reach the faulty machine site;
All parts in contact with raw materials are made of stainless steel to prevent raw materials from being contaminated;
It can be installed directly on the machine or with an optional tripod installed next to the machine (including pneumatic discharge valve).
Optional components
Hopper low material level alarm switch;
Suction control 1/0 module;
Pneumatic discharge valve (used to directly install the platform or shelf above the machine);
Tripod, pneumatic discharge valve, storage bucket and suction box (for tripod mounting type);
Ethernet interface, MODBUS, PROFIBUS communication module can realize remote monitoring and data exchange with extruder, injection molding machine and other hosts.
Gravimetric dosing and mixing units are Gravimetric blender equipment directly connected to the production equipment. A variety of raw materials can be added to mix, which can reduce installation costs. Automatic weighing, automatic mixing and mixing,
The masterbatch mixer is suitable for the automatic mixing of new, secondary materials, masterbatch or additives. This series of models uses high-efficiency and energy-saving motors, mixes according to a preset ratio, and automatically converts to speed through the conditions set by the fully digital microcomputer control system, and drives the equipped precision screw to extrude the material. Add the required materials in the output (calendering) sol cylinder, such as: masterbatch, pigment, new material, additives, auxiliaries, etc. The error value is not higher than 1%. The product is divided into two modes, which are suitable for injection molding and extrusion molding. The screw diameter is divided into 6, 9, 12, 15, 18, etc., which can be evolved into a variety of models, providing different output capacities of 0.1-200 kg/h for customers to choose. There are also two-color, three-color and four-color masterbatch machines, which can be matched according to customer needs to meet different occasions and different fields.
It is widely used in the transportation of raw materials in various industries such as food, chemicals, pharmaceuticals, plastics, non-woven fabrics, chemical fibers, and graphite. It is perfectly matched with the hoppers of packaging machines, injection molding machines, shredders, mixers and other equipment.
Batch blender is a Gravimetric blender set according to customer needs.The technical field of agitator design particularly relates to a plastic particle weighing agitator. Including the frame, the frame is equipped with a mixer, the upper part of the mixer is equipped with a feeding device, a filter arranged below the inlet and a weighing device arranged below the filter. The bottom of the mixer is provided with a second motor. The two motors are connected with a rotating shaft, the rotating shaft is provided with a stirring blade, the front end of the stirring blade is provided with a brush, the inner wall of the agitator is provided with a spray tube, and a plurality of spray tubes are provided with nozzles. The utility model adds a filtering and drainage mechanism. Only the finer color masterbatch can pass through, so that the agglomerated color masterbatch can be smoothly discharged from the discharge pipe, and the uniformity of the mixture is improved. In addition, by setting up a weighing device, the amount of each masterbatch can be precisely controlled. In addition, the mixer of the device also has a cleaning function, which is convenient for future cleaning, and is easy to use to a certain extent.
|
Application and design scheme of Gravimetric blender:
The Gravimetric blender is suitable for mixing powder or granular materials in chemical, food, pharmaceutical, feed, ceramics, metallurgy and other industries.
Application of Gravimetric blender in plastic granule
Input each color masterbatch into each hopper on the top of the weighing mixer, set the parameters in the console (control panel), and weigh and measure each color masterbatch to be accurate to the particle size and set the mixing time. Stirring is carried out, and then the materials are automatically output, and the weighing and mixing are completed. Will be automatically entered into another production device! These weighing, batching and mixing tasks will be completed automatically, calculated automatically by the computer, with an accuracy value of 0.01 or particles
|
Application of Gravimetric blender Ceramic Enterprise
Application of Gravimetric blender in ceramic industry. The main raw materials of ceramics are powder and granules. We use multiple hoppers, powder gauges and particle gauges to better solve the batching problem. When mixing, we use a special mixing barrel to mix the agglomerated powder evenly with the particles. The mixing barrel mixes the powder and the particles together to make the ratio and mixing more uniform; due to the large amount of powder used There may be four types of raw materials and powders in the workshop. We will use the separation method of Gravimetric blender and workshop, and adopt pipeline transportation to ensure that the workshop and equipment are not polluted by powder, while extending the service life of the Gravimetric blender and the environmental protection of the workshop ,product quality.
|
Application of Gravimetric blender in injection molding industry
Application of Gravimetric blender in injection molding industry. The main plastic powders and granules in the injection molding industry. We use multiple hoppers, powder meter or particle meter to better solve the batching problem. When mixing, we use a special mixing barrel to mix plastic particles or plastic powder. The mixing barrel mixes the powder or granules together to make the ratio and mixing more uniform. The corresponding sealing system is formulated to ensure that the workshop and equipment are not polluted by dust, and at the same time extend the service life of the Gravimetric blender and the environmental protection and product quality of the workshop.
|
Application of Gravimetric blender in extrusion industry
Application of Gravimetric blender in extrusion industry. The main plastic powder and granule in the extrusion industry. In the production workshop of the enterprise, we use more reasonable equipment installation and equipment connection, and adopt "Internet of Things" and "4.0 Industry" design solutions to save costs and save factory space. We use multiple hoppers, powder meters or granules in one machine. The instrument can better solve the problem of uniform ingredients. A multi-distribution sealed distribution method is adopted to ensure that the workshop and equipment are not contaminated by dust, and at the same time extend the service life of the weighing mixer and the environmental protection and product quality of the workshop.
|
The application of the Gravimetric blender is closely related to the design plan, and the design plan is inseparable from the company's factory structure and raw materials, as well as the company's requirements! Only a reasonable understanding of the company's application of raw materials combined with the company's factory structure can design a good solution, a set of good design solutions to meet the company's production requirements, reasonable application space and cost savings.
|
Operating instructions for Gravimetric blender:
Gravimetric blender operation control panel
1. First plug in the power, then turn on the switch, the machine will start.
2. If the discharge port is not in the desired position, you must gently push the gravity agitator until the discharge port stops at the desired position.
3. Before starting the machine, please check whether the electrical equipment is normal and whether the mixing cylinder cover is tightly closed.
4. After starting the machine, check the equipment console to see if there is any abnormality, you can use the automatic error correction function,
5. Proportioning design parameters for each hopper raw material, (Figure 1, 2, 3, 4, 5, 6)
6. Design parameters for the feed rate of raw materials in each hopper,
7. Carry out the design parameters for the mixing time.
8. Design parameters for the discharging speed of the stirred mixture.
9. The controller is equipped with a standard USB2.0 interface, which can save the mixing ratio data to the U disk, which is convenient for production quality control.
10. Volume mixing measurement method increases the amount of ingredients; with formula storage function, it can store more than 100 groups of formulas at most. Function of hierarchical security code control and alarm history record.
11. When the warning light flashes, please check whether the raw materials have been used up, or enter the system console panel to check whether there is a problem, and correct it in time. (Automatic error correction function) |
Precautions for Gravimetric blender:
1. Before starting the weighing mixer equipment, please check the power supply and whether there is any debris in the hopper. When mixing different raw materials, check whether there are mixed raw materials in the hopper, mixing barrel and unloading barrel.
2. When the machine needs to stop running, please close the program in the PLC console, and then turn off the power supply of the equipment!
3. Clean the machine and its surroundings as required to ensure safety during operation and prolong the service life of the weighing mixture.
4. The console of the weighing mixer does not light up, please check the power supply and power cord;
5. If the raw materials are not evenly weighed, please check whether the raw materials have been connected to the PLC control panel and the screw weightlessness scale, whether the corresponding parameter settings are correct, mixing time, mixing speed, whether the raw materials are weighed and whether the motor is normal;
6. If the funnel is not discharged, please check if the funnel is blocked;
7. The unloading speed is not fast, please check the time set by the PLC console;
8. If you are not a professional related mechanical maintenance personnel, please do not disassemble the machine for maintenance by yourself.
9. For more information, you can consult manufacturers and suppliers of weighing mixers for faster troubleshooting.
|
| |